Understanding Pigging System Application: A Smart Solution for Modern Industries
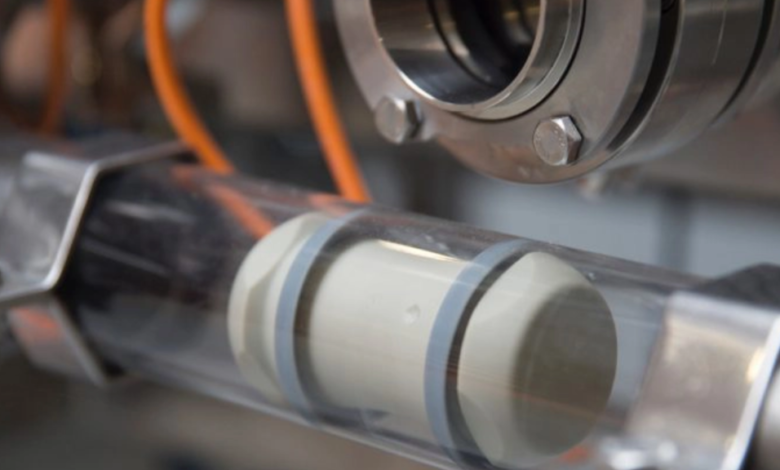
In the evolving world of industrial manufacturing, the emphasis on efficiency, waste reduction, and sustainable processing is more significant than ever. One of the lesser-known yet powerful technologies that contribute to this movement is the pigging system. Although initially developed for the oil and gas sector, the pigging system application has extended far beyond its original roots. Today, it is actively transforming operations across a wide range of industries including food, cosmetics, chemicals, paints, and pharmaceuticals.
In this article, we’ll dive deep into what a pigging system is, explore its key applications, and highlight the benefits it offers in modern processing environments.
What is a Pigging System?
A pigging system is an arrangement that utilizes a device called a “pig” to travel through pipelines. This pig scrapes the inside of the pipe, pushing out residual product and cleaning the interior. It’s usually propelled by compressed air, nitrogen, or liquid pressure.
The system typically includes:
- Pig Launchers and Receivers
- Pipeline and Control Valves
- Pig Detection Sensors
- Air/Gas Supply Units
- Control Systems (Manual or Automated)
The core purpose of any pigging system application is to maximize product recovery, reduce waste, minimize cleaning needs, and ensure efficient transition between different production batches.
See also: The Strategic Advantage of Partnering with a china screw manufacturer
The Growing Importance of Pigging System Application
Traditionally, pigging was associated with long-distance oil and gas transport. However, modern industries with batch production and high product value have found pigging systems to be highly beneficial.
With global pressures on resource conservation and operational sustainability, pigging has become an attractive solution. It supports cost savings, reduces environmental impact, and ensures compliance with hygiene and safety standards.
Key Pigging System Applications Across Industries
Let’s explore how pigging system application varies across several key industries:
1. Food and Beverage Industry
In food manufacturing, strict hygiene regulations and high-value products make pigging systems highly useful.
Applications include:
- Recovery of leftover product such as sauces, dairy, juices, and syrups
- Cleaning of pipelines between batches (e.g., from strawberry to mango puree)
- Reducing water and chemical consumption in clean-in-place (CIP) systems
By using pigging systems, food processors can recover up to 99.5% of product left in the line—translating into thousands of dollars in savings every month.
2. Cosmetics and Personal Care
Manufacturers of lotions, creams, gels, and shampoos rely on pigging systems for hygiene and cost-efficiency.
Use cases include:
- Batch separation in production lines
- Avoiding contamination from scents and active ingredients
- Minimizing expensive product loss during transfers
Given that many cosmetic products are viscous and sensitive to contamination, a pigging system helps maintain product quality and reduce cleaning effort.
3. Chemical and Specialty Fluids
Handling hazardous or high-cost chemicals requires precision. In these environments, pigging system application improves safety and material handling.
Common applications:
- Recovering resins, polymers, solvents, or adhesives
- Minimizing human contact with hazardous substances
- Ensuring safe transitions between chemically reactive batches
Chemical companies also reduce disposal and cleaning costs with the integration of an automated pigging system.
4. Paints, Coatings, and Inks
Pigging is essential in paint and ink industries due to frequent color changes and the sticky nature of these products.
Main applications:
- Recovering residual paint from pipelines
- Eliminating solvent flushing for cleaning
- Reducing color contamination during batch changes
By using pigging, companies significantly lower their VOC emissions and meet regulatory standards while increasing yield.
5. Pharmaceutical and Nutraceutical Industry
Pharmaceutical production requires a sterile, highly controlled environment. Pigging systems are tailored to meet these strict requirements.
Pigging system application includes:
- Cleaning and recovering oral suspensions, syrups, and ointments
- Maintaining product integrity between batches
- Ensuring GMP compliance and traceability
Advanced systems in this industry often include automated controls and stainless-steel pigs suitable for sanitization and sterilization.
Advantages of Pigging System Application
The implementation of a pigging system brings several strategic advantages:
✅ Product Recovery
Rather than flushing valuable products down the drain, pigging systems help recover nearly all of the residual product left in the lines.
✅ Reduced Downtime
Pigging dramatically shortens the time required for changeovers between batches, improving operational efficiency and uptime.
✅ Improved Hygiene
In food, cosmetic, and pharma industries, pigging ensures sanitary pipeline conditions and reduces the chance of cross-contamination.
✅ Lower Cleaning Costs
Less water and fewer cleaning chemicals are needed since pigging removes the majority of the product before cleaning even begins.
✅ Environmental Sustainability
Pigging supports waste reduction, water conservation, and better energy efficiency—key components of corporate environmental goals.
Automation and Modern Pigging Systems
Modern pigging systems often include PLCs (Programmable Logic Controllers) or SCADA systems for automation. This enables:
- Real-time pig tracking
- Automated batch changeovers
- Remote monitoring and diagnostics
- Seamless integration into existing plant control systems
For industries with complex production lines, automation maximizes the return on investment and ensures repeatable, safe pigging processes.
Real-World Case Study
A leading sauce manufacturer installed a pigging system on its filling line, which handled tomato-based and creamy sauces.
Before Pigging:
- Product loss of 5 liters per batch
- Frequent contamination during changeovers
- Cleaning required 20 minutes per switch
After Pigging:
- Product recovery increased to 98%
- Changeover time reduced to under 5 minutes
- Cleaning agent usage cut by 70%
The company saw a full ROI in under a year, proving how a single pigging system application can drive significant improvements.
Things to Consider When Implementing a Pigging System
Before integrating pigging into your process, consider the following:
- Type of product: Viscosity, temperature, and chemical properties affect pig design
- Pipeline layout: Straight runs are best, though pigging can be adapted to complex geometries
- Sanitary requirements: Especially in food and pharma, materials must meet industry regulations
- Batch frequency: High-frequency changeovers benefit most from pigging
- Control requirements: Manual or fully automated systems depending on plant scale and budget
Final Thoughts
A well-planned pigging system application is more than just a cleaning method—it’s a comprehensive solution for boosting efficiency, improving product yield, maintaining hygiene, and achieving environmental goals. Whether in sauces, creams, coatings, or chemicals, pigging technology continues to prove its versatility and value.
As industries strive to stay lean, safe, and sustainable, pigging systems are not only a good investment—they’re a necessity for modern production lines.