Exploring the Essential Role of Metal Surface Treatment Companies in Modern Industry
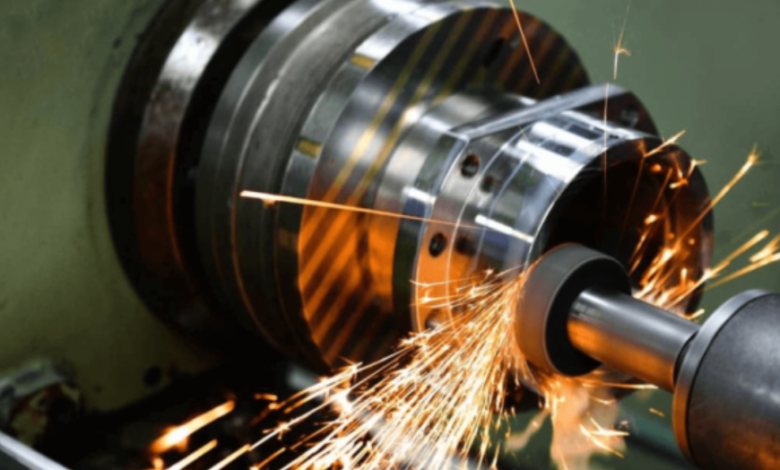
In the realm of industrial manufacturing, performance and durability are paramount. Whether it’s aerospace components, automotive parts, or tools used in heavy machinery, metals must withstand extreme conditions without degrading over time. This is where metal surface treatment companies play a vital role—enhancing the properties of metal surfaces to extend lifespan, boost performance, and improve aesthetics.
With rising demand for corrosion resistance, wear resistance, electrical conductivity, and decorative finishes, metal surface treatment companies have become indispensable partners across multiple sectors. This article offers a comprehensive look at the importance of these companies, the techniques they use, and the industries they serve.
What Do Metal Surface Treatment Companies Do?
metal surface treatment companies specialize in modifying the external layer of metal components to enhance their physical, chemical, and mechanical properties. These treatments can be either chemical, electrochemical, mechanical, or thermal.
The primary objectives of metal surface treatment include:
- Protecting metal from corrosion and oxidation
- Increasing hardness and resistance to wear
- Improving adhesion for paints or coatings
- Enhancing electrical or thermal conductivity
- Creating a more appealing surface finish
By offering customized surface treatment processes, these companies ensure that metal parts meet the specific demands of their applications.
See also: self loading mixer: The Evolution of Concrete Mixing Technology on Construction Sites
Common Techniques Used by Metal Surface Treatment Companies
Each industry and application calls for unique surface characteristics. As such, metal surface treatment companies employ a wide array of techniques:
1. Electroplating
One of the most popular methods, electroplating involves using an electric current to coat a metal surface with a thin layer of another metal (e.g., zinc, nickel, or chromium). This enhances corrosion resistance and appearance.
2. Anodizing
Primarily used for aluminum, anodizing thickens the natural oxide layer on the metal surface. It improves corrosion resistance, offers a base for dyes, and adds electrical insulation.
3. Powder Coating
Powder coating provides a decorative and protective finish. The powder (made of resin and pigment) is applied electrostatically and then cured under heat, forming a hard, uniform surface.
4. Galvanizing
Galvanization is the process of coating metal—typically steel or iron—with a protective layer of zinc to prevent rusting.
5. Passivation
Used especially on stainless steel, passivation removes free iron from the surface, enhancing the formation of a passive oxide layer that resists corrosion.
6. Phosphate Coating
Often used as a pretreatment for painting or lubrication, phosphate coatings provide good adhesion and wear resistance.
7. Laser Surface Hardening
A more advanced treatment, this uses laser technology to locally harden specific areas on a metal component without affecting its overall structure.
Importance of Metal Surface Treatment Companies in Different Industries
The applications of metal surface treatment companies span numerous sectors, each with unique requirements:
Automotive Industry
Vehicles demand components that can resist corrosion, endure high temperatures, and maintain structural integrity. Surface treatments are used on body panels, engine parts, suspension components, and brake systems.
Aerospace and Defense
Aircraft and defense equipment are exposed to extreme environments. Metal surfaces must be lightweight yet durable, resistant to oxidation, and capable of maintaining structural strength at high altitudes.
Construction and Infrastructure
From steel beams to scaffolding, metal structures used in construction require treatments that enhance their longevity and resistance to weather elements.
Medical Equipment
Surgical instruments, implants, and diagnostic equipment often undergo treatments to meet hygienic standards, resist corrosion from bodily fluids, and offer smooth finishes.
Electronics and Electrical
Components such as circuit boards, connectors, and enclosures are treated to improve conductivity, EMI shielding, and prevent oxidation of conductive surfaces.
How Metal Surface Treatment Enhances Sustainability
Modern metal surface treatment companies are also contributing to the sustainability movement. By extending the life of metal parts, they reduce the need for replacements and minimize resource consumption.
Additionally, many companies are adopting eco-friendly treatments, such as water-based coatings and low-VOC (volatile organic compounds) methods. Innovations like trivalent chromium plating and recyclable powder coatings are replacing more toxic legacy processes.
This shift toward green surface treatments not only protects the environment but also helps manufacturers comply with increasingly stringent environmental regulations like REACH and RoHS.
Choosing the Right Metal Surface Treatment Company
Not all service providers are equal. Selecting the right metal surface treatment company can make a significant difference in product quality and lifecycle. Here’s what to consider:
1. Certifications and Standards
Look for companies that comply with ISO 9001, AS9100 (for aerospace), or IATF 16949 (for automotive). These ensure quality management and process consistency.
2. Technical Expertise
The ideal company should have experience with different base metals and treatment methods. They should also be able to recommend the best process for your application.
3. Customization Capabilities
From prototype runs to high-volume production, flexibility in batch size and finishing type is crucial.
4. In-house Testing and Quality Assurance
Advanced testing methods like salt spray testing, adhesion testing, and microhardness measurement ensure the treated parts meet your standards.
5. Lead Time and Cost-efficiency
While quality is essential, timely delivery and competitive pricing are equally important in keeping production schedules on track.
Trends Shaping the Future of Metal Surface Treatment Companies
Several key trends are shaping the growth and evolution of metal surface treatment companies:
1. Automation and Industry 4.0 Integration
Smart manufacturing has entered the surface treatment domain. Robotic coating arms, sensor-based quality control, and AI-driven process optimization are becoming more prevalent.
2. Digital Twin Technology
Some advanced companies now create digital models of parts and simulate surface treatment outcomes before the actual process. This improves efficiency and accuracy.
3. Nano-Coatings
Ultra-thin protective films developed at the nanoscale are offering unprecedented benefits in terms of hardness, conductivity, and chemical resistance.
4. Outsourcing and Globalization
With the rise of global supply chains, manufacturers often partner with metal surface treatment companies across borders. China, India, and Eastern Europe have become hubs for outsourced finishing services.
Final Thoughts
From enhancing durability to boosting visual appeal, the contribution of metal surface treatment companies to modern manufacturing is irreplaceable. Their services are not just about making metals look better—they’re about optimizing performance, ensuring safety, and delivering long-term value.
As industries continue to innovate and expand, the demand for high-quality surface treatments will only increase. Choosing a reliable, forward-thinking treatment partner will be critical for manufacturers who aim to maintain a competitive edge.